Patented Dry Ingredient Dispensers by I.M.
Ingredient Masters dry ingredient dispensers are manufactured from rotationally molded polyethylene and provide performance that is superior to steel or stainless steel dispensers. Our dry ingredient dispensers have a liquid-smooth interior which, combined with the dispenser’s geometry, provides excellent flow characteristics. Polyethylene dispensers have exceptional durability, and remain “sweat-free” when temperatures fluctuate.
Benefits of Our Dispensers
Rotationally Molded
Rotational molding gives plastic storage tanks a unique combination of strength, light weight and reasonable cost. The seamless rotomold construction also makes them easy to clean and leak-proof.
Multiple Sizes
We Offer Dispensers from 3.5 Cuft to 100 Cuft, In a variety of shapes and sizes to maximize flow while conserving space and improving ergonomics.
Food Grade Materials
Made from raw materials that are USDA, FDA, and 3A Dairy compliant. Material is chemically inert, non-conducting, and do not impart taste or odor.
Virtually Zero Maintenance
High resistance to acids, alkalis and abrasives while having long-term resistance to impact and stress cracking (ESCR) and high tensile strength.
See your Product
Natural color of the resin makes them translucent, so that the level of material inside is easily visible
Inventory Rotation
(FIFO) First in First Out Principle reduces the need for clean-out of dispensers.
Natural Insulator
Provide barrier to moisture, gases and vapor, and with the addition of UV stabilizers for lasting performance.
ATEX CERTIFIeD
Dispensers can be made conductive to meet ATEX certifications.
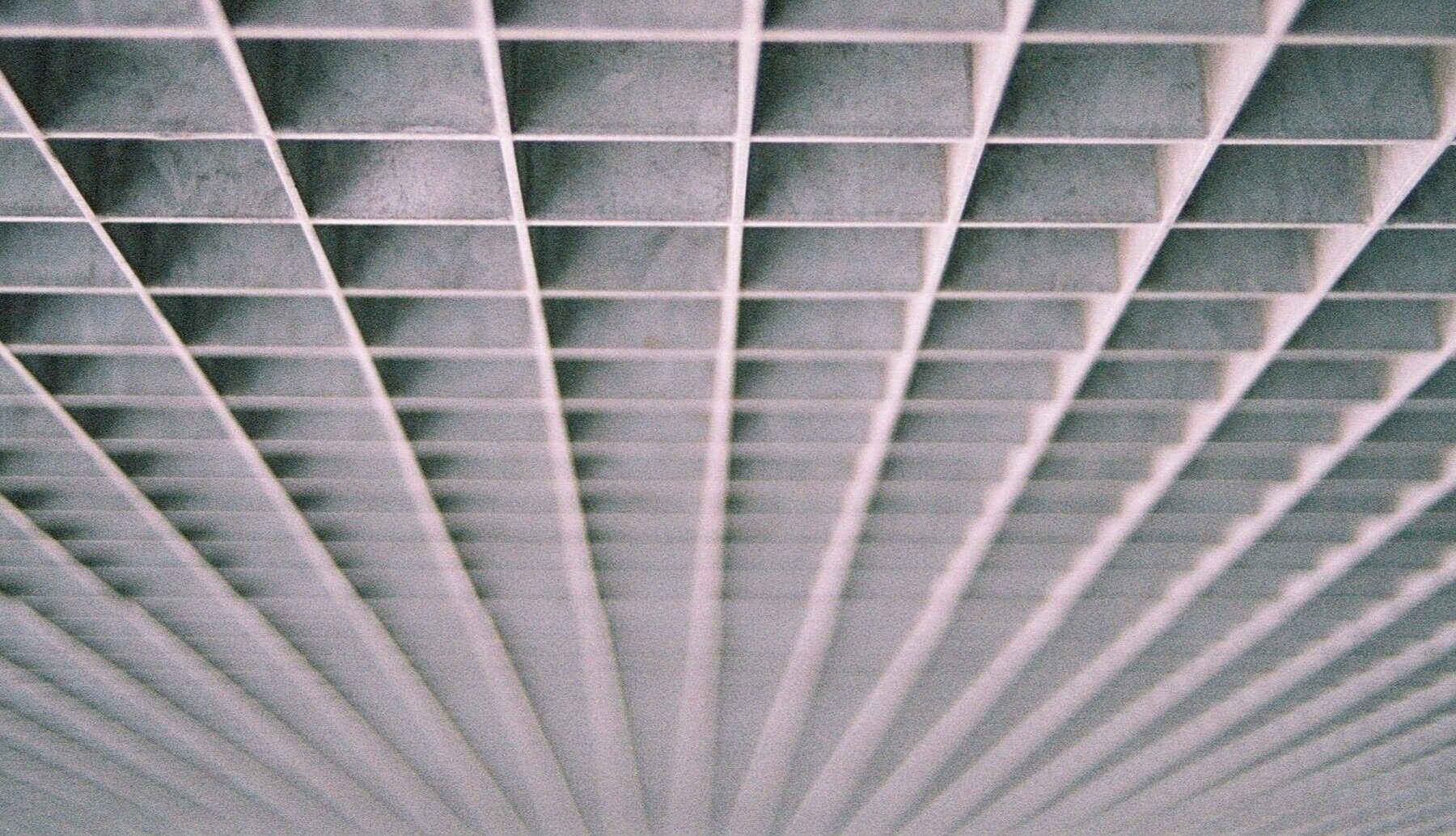
Multi-Use Applications
Small Use
Small Square Dispensers range from 3.5 Cut to 15 Cuft. Their small foot print makes them suitable for micro-adds or lab-adds or a surge hopper for packaging material.
Paper Bags
These medium size dispensers are rectangular in shape with rounded corners. They are offered in 15 to 25 Cuft. sizes to handle most paper bag applications.
Bulk Bags
Ranging from 30 Cuft. to 80 Cuft. These Round Dispensers are ideal for receiving materials from Bulk Bags.